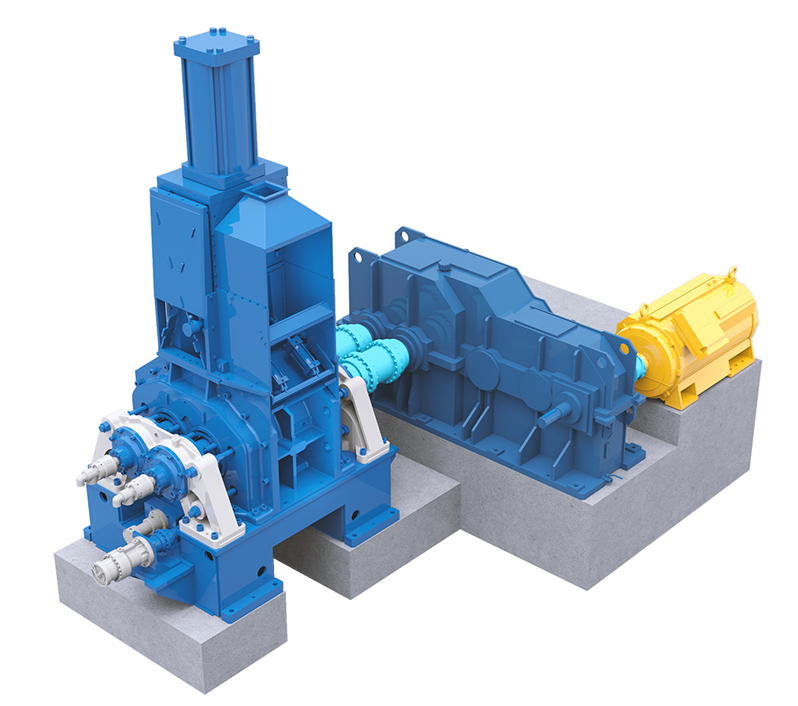
Internal Mixer
The specific design of the McNeil Repiquet Internal Mixer allows our customers to produce High-Quality compounds at the best production price. McNeil Repiquet’s Internal Mixer can achieve a mixing of rubber and plastic compounds with optimal conditions regarding energy consumption and quality requirements.
Its design is based on four following characteristics:
- Special Intermeshing rotors
- Strong mechanical design with High Life me Material
- Wide Thermic exchange surface between the compound and inner mixing chamber
- Onboard and up-to-date control giving an opmum control of the process
These advantages allow:
- To highly increase the installed power capacity
- To have a better use of power for rotor speed and compound pressure
- To control compound temperature all along the cycle time
- To optimize the working cycle me
ROTORS
Rotors are designed in helical form with embossments. They rotate at the same speed. The compound is worked through the interfering profile of the rotors while rotating giving lamination, friction and lateral transfers in opposite directions.
We bring a high-quality control in the manufacturing of the rotors, especially on the dimensions after machining, surface treatment and assembly but also on the material quality choice. Hollow bodies are poured with CrMn Steel and their edges covered by Stellite, then they are assembled and solidly pin-joined on hollow shafts in Mn Steel. Inner water flow through the rotor allows controlling the com-pound temperature. According to this design, mixing is achieved without shearing and deterioratuon, powders are spread by the compression between the profiles of the rotors without any risk to burn the compound, either for rubber or for plastic (PVC).
POWER TRANSMISSION
Several combinations are technically offered. According to the configuration of the rotor the most common is based on one gearbox with one inlet and 2 outlets. The gearbox is driven by high efficiency AC motor (driven by an inverter) allowing to reduce the efforts on the mechanical parts and allowing to optimize the recipes.
COOLING SYSTEM
Each element, of the mixing chamber (See schematics on the left side) offers a very wide thermic exchange surface (Heating or cooling). This about 30% higher in comparison with all the other types of internal mixers. The principal advantage of this added value is time-saving. For example, a faster rubber mixing process is usually carried out in 2 stages in a traditional mixer, whereas the process only requires one single operation in the internal mixer. Its outstanding combinations make it possible to stabilize the temperature below the temperature critical level. On the other hand, for the pre-gelling of a PVC mixture, the intake of calories essential for this operation is given very precisely in a limited time.
DESIGNED FOR EASY MAINTENANCE
The “McNeil Repiquet” internal mixer is designed to work efficiently at very high rates. Its compact design has been efficiently studied to contribute to ensuring safety parameters, but also to enhance life-time durability and to decrease maintenance costs, and this is possible because:
- the rotors are mounted directly on the bearings with double rows of rollers which are independent of the main tank
- the space between the flange and the bearings allow an easy access to the sealing device
- the wear plates can be easily swapped without dis-mantling the bearings
The picture on the right side shows the accessibility of the main components (tank flange, rotors, bearings, etc.) If necessary, in the case where the internal mixer is used for abrasive mixtures such as those used in the manufacture of floor tiles or ferrite-loaded rubber, the rotors can be easily reloaded by welding of Stellite.
Types of accessories and optional equipment:
Stellite faced rotors and wear plates, lined chamber, water/Steam piping, injection pumps and pump unit, temperature recorders, guillotine hopper, side feeds openings, exhaust hood.
Internal mixers for rubber
Model Reference | R10 | R30 | R50 | R110 | R200 | |
Free volume of the chamber (in liters) | 16 | 40 | 82 | 160 | 320 | |
Useful volume of the chamber (in liters) | 8 à 12 | 24 à 30 | 45 à 60 | 85 à 115 | 150 à 230 | |
Power base (in CV) recommended at nominal torque for a rotor speed of: | 50 tr / mn 100 tr / mn | 80 16 | 200 40 | 500 82 | 1000 160 | 1700 320 |
Weight with gable cage (in tons) | 12 | 15 | 23 | 50 | 70 |
Internal mixers for plastics
Model Reference | R10 | R30 | R50 | R110 | R200 | |
Free volume of the chamber (in liters) | 16 | 40 | 82 | 160 | 320 | |
Useful volume of the chamber (in liters) | 8 à 12 | 24 à 30 | 45 à 60 | 85 à 115 | 150 à 230 | |
Power base (in CV) recommended at nominal torque for a rotor speed of: | 50 tr / mn 100 tr / mn | 60 90 | 150 220 | 350 500 | 700 1000 | 1000 1500 |
Weight with gable cage (in tons) | 12 | 15 | 23 | 50 | 70 |
The above useful volumes, speeds and powers are only indicative and may vary depending on the nature and physical state of the mixture, the loading process, etc.