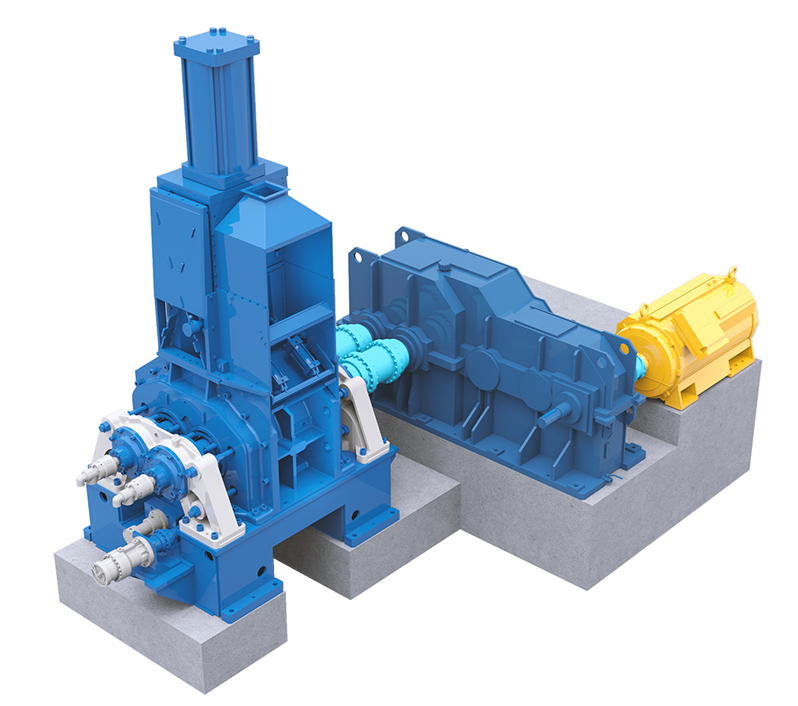
Mélangeur Interne
La conception originale du mélangeur interne « REPIQUET » permet la production de mélanges de haute qualité aux meilleurs coûts de fabrication.
Ce mélangeur interne réalise dans les meilleures conditions le malaxage et l’homogénéisation des mélanges de caoutchouc ou de plastiques.
Le rendement moyen du mélangeur interne « REPIQUET » est ainsi supérieur d’environ 30% à celui des mélangeurs internes traditionnels.
Son originalité de conception peut se résumer par les caractéristiques suivantes:
- Rotors spéciaux à profils interférents
- Dimensionnement du piston presseur,
- Construction robuste des différents ensembles mécaniques,
- Très importante surface d’échanges thermiques entre la matière et tous les éléments constitutifs de la chambre de mélange
Ces avantages ont permis:
- D’augmenter considérablement la puissance installée,
- D’utiliser cette puissance pour l’augmentation de la vitesse des rotors et de la pression sur le mélange,
- De réduire les cycles de travail à des temps extrêmement courts, et d’accroitre ainsi la production,
- D’assurer une excellente homogénéisation même en sous-charge – le chargement peut donc se faire progressivement sans aucune perte de la qualité du mélange.
Les Rotors
Les rotors, en forme d’hélice et munis de bossages, sont entrainés à vitesse égale. Leurs profils interférents travaillent le mélange par laminage, friction et transferts latéraux en directions opposées. La réalisation des rotors fait l’objet de contrôles sévères et les matériaux les plus appropriés ont été choisis. Les corps creux sont coulés en acier au chrome-manganèse, usinés, stellités sur les arêtes de bossage, puis emmanchés et goupillés sur des arbres creux en acier manganèse. Une circulation de fluide tempère les rotors au cœur même de la masse en mélange. Grâce à cette conception, le mélange s’effectue sans cisaillement ni dégradation. Les poudres sont dispersées par compression entre la périphérie de l’hélice, les bossages d’un rotor et le corps du rotor opposé.
La Cuve
La cuve en acier est constituée d’éléments – coquilles et flasques – dont toutes les parois internes sont conditionnées pour la circulation du fluide de régulation de température (eau ou vapeur). Chacun d’entre-eux pouvant être alimenté séparément. Les flasques de cuve sont pourvus de plaques d’usure en fonte trempée à huile résistance à l’abrasion.
En option: le reste de la cuve peut être également équipé de fourrures d’usure interchangeables.
Presseur
Cet organe est commandé par vérin pneumatique. La pression désirée peut être sélectionnée à partir du poste de commande. La large surface du presseur permet de travailler à une pression modérée adéquate et de maintenir l’étanchéité parfaite de la cuve. Comme tous les éléments constitutifs de la chambre, le presseur à double paroi contribue aux échanges thermiques.
Porte de vidange basculante
Actionnée à partir d’un groupe hydraulique, la porte de vidange basculante à dégagement total est manœuvrée par vérin hydraulique. La fermeture est effectuée par 2 doubles verrous. La selle, elle-même est à double paroi. Ce système réduit valablement les temps d’évacuation des mélanges et donne une étanchéité parfaite de la partie inférieure de la cuve.
Garnitures d’étanchéité
Au passage des arbres de rotor, les flasques de cuve sont équipés de dispositifs d’étanchéité à fuite interne ou externe. La lubrification est assurée à haute pression par un fluide qui établit un courant d’évacuation des particules de mélange susceptibles de s’insérer dans le dispositif.
Tous les éléments de la chambre de mélangeage (schéma ci-contre) offrent une très importante surface susceptible d’être chauffée ou refroidie. Celle-ci est supérieure d’environ 30% par rapport à la moyenne des mélangeurs internes traditionnels (précision de température +/- 2°C). Cette caractéristique fondamentale engendre des gains de temps précieux. Par exemple, un mélange de caoutchouc accéléré, généralement réalisé en deux temps dans un mélangeur traditionnel est dans de nombreux cas, effectué en une seule opération dans le mélangeur interne. Ses possibilités exceptionnelles permettent de stabiliser la température en dessous de l’échauffement critique. Par contre, pour la pré-gélification d’un mélange de P.V.C. l’apport de calories indispensables à cette opération est donné très précisément en un temps limité.
Afin d’assurer d’une façon continue et contrôlée les températures de travail, nos mélangeurs sont livrés, sur demande, avec un groupe de thermorégulation ayant plusieurs circuits indépendants pour cuve, rotors, presseur et porte basculante.
Le mélangeur interne « REPIQUET » est conçu pour travailler efficacement à des cadences très élevées. Sa conception de base contribue à sa sûreté, à sa résistance à l’usure et à son faible coût d’entretien :
- Montage des rotors sur paliers à double rangée de rouleaux indépendants de la cuve,
- Montage des rotors sur paliers à double rangée de rouleaux indépendants de la cuve,
- Permutation aisée des plaques d’usure sans démontage des paliers
Le schéma ci-contre démontre l’accessibilité des principaux organes (flasques de cuve, rotors, paliers…) Si nécessaire dans le cas où le mélangeur interne est utilisé pour des mélanges abrasifs tels que ceux employés dans la fabrication de dalles de sol ou caoutchouc chargé ferrite, les rotors peuvent être aisément rechargés par soudure de stellite.
Mélangeurs internes pour caoutchouc
Modèles | R10 | R30 | R50 | R110 | R200 | |
Voluwme libre de la chambre (en litres) | 16 | 40 | 82 | 160 | 320 | |
Volume utile de la chambre (en litres) | 8 à 12 | 24 à 30 | 45 à 60 | 85 à 115 | 150 à 230 | |
Base de puissance (en CV) préconisée au couple nominal pour une vitesse de rotors de: | 50 tr / mn 100 tr / mn | 80 16 | 200 40 | 500 82 | 1000 160 | 1700 320 |
Poids avec cage à pignons (en tonnes) | 12 | 15 | 23 | 50 | 70 |
Mélangeurs internes pour plastiques
Modèles | R10 | R30 | R50 | R110 | R200 | |
Voluwme libre de la chambre (en litres) | 16 | 40 | 82 | 160 | 320 | |
Volume utile de la chambre (en litres) | 8 à 12 | 24 à 30 | 45 à 60 | 85 à 115 | 150 à 230 | |
Base de puissance (en CV) préconisée au couple nominal pour une vitesse de rotors de: | 50 tr / mn 100 tr / mn | 60 90 | 150 220 | 350 500 | 700 1000 | 1000 1500 |
Poids avec cage à pignons (en tonnes) | 12 | 15 | 23 | 50 | 70 |
Les volumes utiles, vitesses et puissances ci-dessus ne sont donnés qu’à titre indicatif et peuvent varier en fonction de la nature et de l’état physique du mélange, du processus de chargement, etc.
Tous nos mélangeurs internes peuvent être équipés d’un module autonome de pilotage et de contrôle automatique du cycle de mélange offrant les caractéristiques et avantages suivants:
- Souplesse maximum pour la formulation,
- Enregistrement et/ou impression de tous les paramètres et événements par cycle de mélange,
- Plusieurs choix possibles d’asservissement : température, temps, puissance,
- Répétition des paramètres du mélangeage,
- Optimisation de la dispersion des mélanges
- Optimisation de la dispersion des mélanges
Ce module de pilotage comprend essentiellement :
- Un automate programmable pour les fonctions logiques : changement, séquences du cycle, ainsi que le mode d’asservissement,
- Un bloc de gestion de commande pour enregistrement des différents paramètres,
- Un bloc FORMULES avec capacité mémoire de stockage suivant la taille.