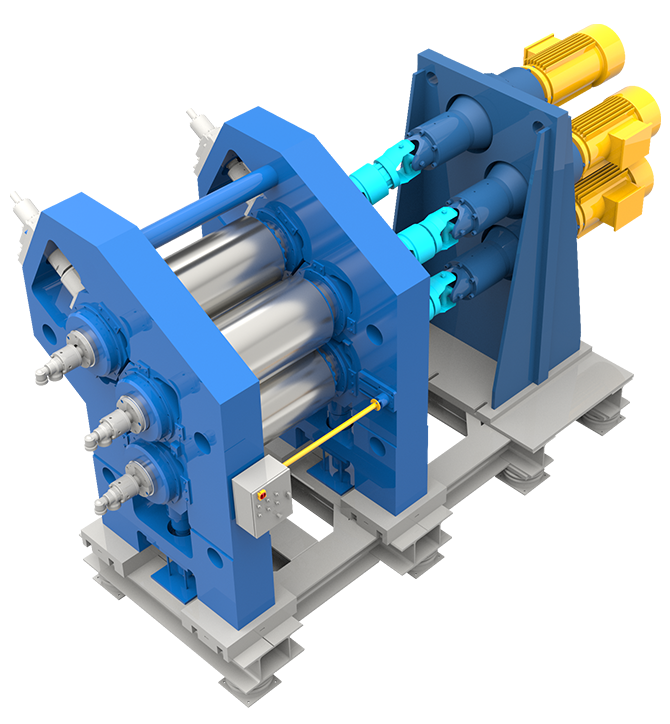
Calenders
Using appropriate technique, we are offering tailor-made equipment meeting the requirements of every rubber processor.
Depending upon the material to be calendered and the most suitable sheet path, the customer has the choice between a variety of solutions regarding calender type and size, roll design, drive, roll-deflection compensation, control and automation.
Calender Rolls
The rolls are made of chilled cast iron with a surface hardness of 480 to 500 Brinel.
According to calender size and the material to be calendered, chambered, or cored and drilled rolls are used. The latter offers the best system for heating medium circulation. As the passages are drilled right to the neck of the roll, local heat exchange is increased, and cooling or heating is ensured under the most favourable conditions.
Roll Bearings
The calender rolls are mounted either on smooth bush bearings or on conical or cylindrical roller bearings.
Side Frames
The side frames of the modern calenders are of high-resistant cast iron or steel with tubular cross-section and joined by a sturdy top link.
As for the other parts of the machine, their weight and dimensions are more than adequately calculated in order to ensure smooth running and to minimize deformation under maximum production loads.
The frames are specially designed with side windows to enable easy mounting and dismounting of the rolls and bearings.
Current types of calenders for rubber processing
Nip Adjustment
The movable rolls are set by two independent nip-adjusting gears providing either rapid opening or closing or fine adjustment (as slow as 12 mm/min.). If desired, one or more rolls can be geared to sheet-thickness gauges.
The gap between the rolls is indicated electronically through digital instruments with a scale division of 0.01mm.
For the specific case of doubling at constant pressure on two or four-roll machines, the bearings of the last roll or rolls can be fitted with hydraulic cushions combined with the conventional regulating devices.
This system also facilitates the passage of seams and the like.
Roll Preloading
Clearance in the bush or cylindrical roller bearings as well as in the nip-adjusting gears is eliminated by a system of cylinders which maintain the rolls under loading in normal working position.
In the case of conical roller bearings with preset clearance, another pull-back system only eliminates the clearance of the nip-adjusting screws.
Safety Devices
Calenders are obviously equipped with all necessary safety devices for the protection of the operators (Emergency braking through safety bars and wires, sound warning system for signaling machine trouble, safety guarding of all moving parts).
Upon request, calenders are equipped with a device monitoring the bearing temperature. The temperature of each bearing is shown in turn on the control console and limit temperature is signaled by a warning device.
In addition, strain gauges can be provided for measuring bearing load.
Apart from the above-described improvements to modern calenders, our engineers and technicians have developed combinations of special devices for compensating roll deflection during calendaring in relation the initial cambered or cylindrical profile.
These devices are mounted on opposite rolls and enable the processor to combine the correction curves in order to obtain the most favorable roll profile for each calendering job.
Cross-Axis Adjustment
This device operates on the principle of crossing the center lines of two rolls in order to compensate for roll deflection. The cross-axis movement is obtained by 2 motorized adjusting gears moving the bearing blocks in the side frames. Cross-axis roll adjustment enables a profile correction of up to 0.20 mm.
Roll Bending
Roll bending operates on the principle of cambering the roll in direction of adjustment in order to compensate for deflection of the initial profile. This is done by applying with hydraulic cylinders, a force to ancillary bearings located on the roll necks outside the main bearings.
Convex or concave roll bending enables an adjustable compensation for roll deflection.
Bearing Lubrication
Regular bearing lubrication is essential in order to avoid wear, seizing and any trouble which would require the stopping of the calender line.
Before starting the lubricating circuit, the oil is brought to temperature by controlled heating of the tank.
The lubricating system of our calenders also allows for perfect control of bearing temperature. The lubricating oil is recirculated after being filtered and cooled in order to avoid oxidation.
Besides all the elements for oil circulation, temperature, flow and pressure control, the lubricating circuit includes a visual and sound warning device which signals any lubrication failure.
The bearings are designed for leak-proof operation.
Drive
Roll drive is more and frequently through a gear box containing all the speed-reducing elements.
The gear box can be driven by a single constant – or variable speed moto, or the gearing of each roll can be driven independently by a variable – speed motor.
The latter drive system allows for immediate adjustment of the friction according to the compound to be calendered. Spped ratios can normally vary between 1 and 0.5 of nominal speed of pilot roll.
Universal couplings connect gear box and calender rolls without apparent energy loss, whatever the nip setting for the various materials to be calendered. That eliminates vibrations and subsequent risks of defects on the sheet.
Roll temperature control
Thermal fluid, as heating medium is circulated at high speed through the rolls, permitting rapid heating or cooling while avoiding thermal shocks.
With drilled rolls, temperature regulation can be completely automated by electronic control of the valves.
Regular accuracy is of +/- 1degC over the entire roll face.