Example 1
Context: Customer request for a refurbishment of a 550×1500 mixing tool. Objective: Automatic hydraulic modernization of nip adjustment on the external roll of a 550 x 1500 mixer with rapid safety return.
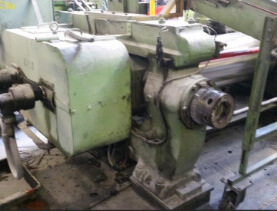
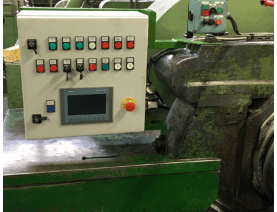
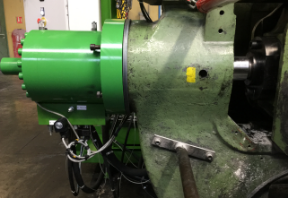
Design of a new hydraulic cylinder system instead of a manual adjustment. Encoder and distributor are mounted directly on the cylinder. Design of a new support on the bearing housing.
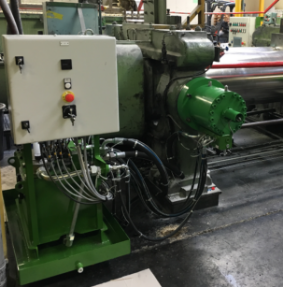
New nip adjustment control cabinet fully compatible and integrated with the production line process supervisor.
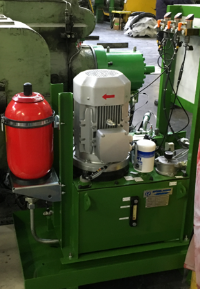
Hydraulic control unit provided with safety accumulator to be able to open the roll adjustment in case of an emergency and if electrical power shuts down.
Example 2
Objective: Mechanical modernization and update of the security (up to date regulation norms) of nip adjustment on external roll mill 700 x 2200.
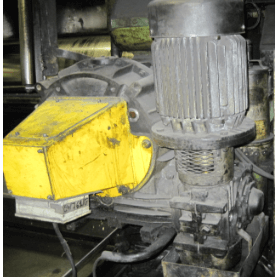
electrical motor + gearbox
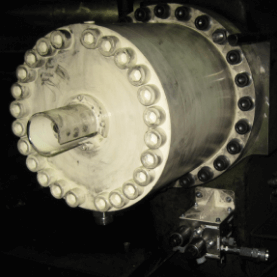
hydraulic cylinder
Replacement of old system of electrical motor + drive with copper nut and screw on the frame with a new hydraulic cylinder, with adapted support for bearing housing, cylinder fixation and hydraulic power unit.
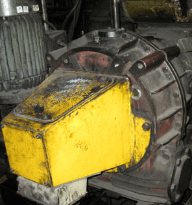
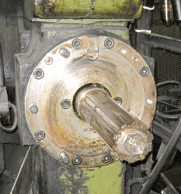
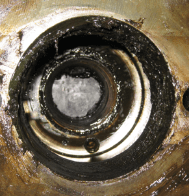
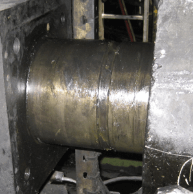
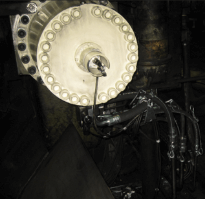
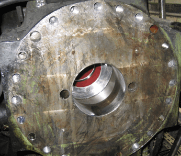
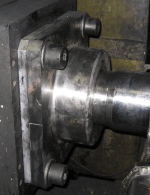
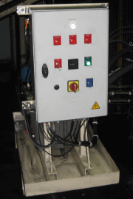
Example 3
Objective: Modernization and commissioning of an old calender 4 rolls 300×500 in Z partially dismounted in order to use it in new calendering line.
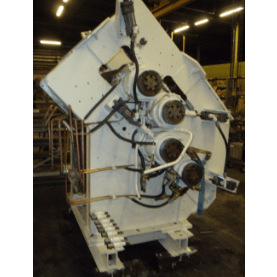
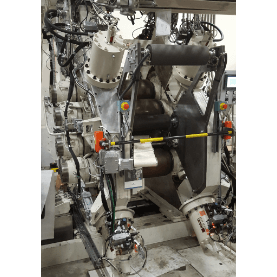
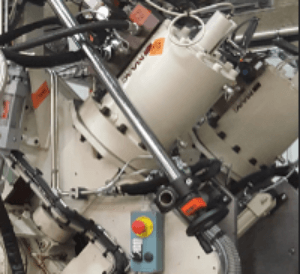
Rolls gap adjustment with hydraulic cylinder and support (instead of gearmotor system) with hydraulic distributor mounted on the cylinder to limit possible hydraulic leakage between hydraulic unit and cylinder.

Stock guide system from fix system on roll 1 to mobile system on roll 2.
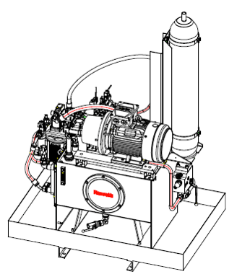
Hydraulic power unit for nip adjustment and roll temperature control unit.
Example 4
Objective: Full Calender modernization – 3 rolls vertical 450 x 1100.
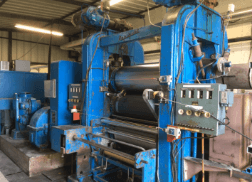
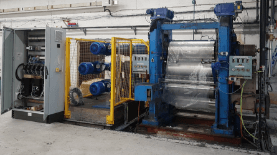
Modernization of motor+gearbox drive of nip adjustment and textile tension screw.
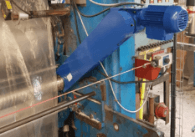
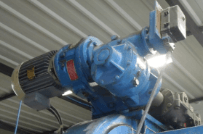
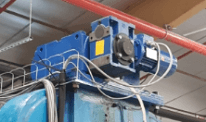
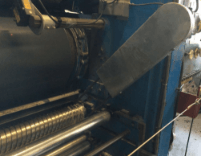
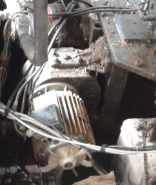
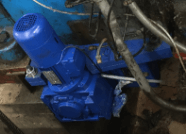
Replacement of roll drive : old system made by DC motor+gearbox and on customer request replacement of a gearbox with big and small wheel mounted on 3 gears by 3 planetary gearboxes + motors.
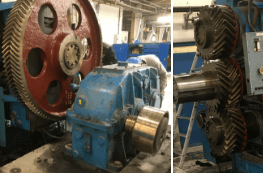
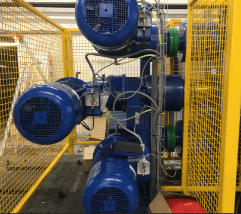
Modernization of the control command from relay technology to PLC + electronic drives + HMI and security element to drive the calender according to actual international norms.
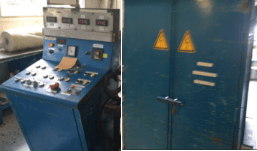
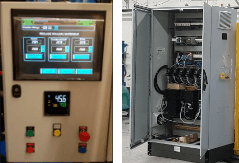
Frame stress calculation with finite element analysis
Objective : Frame stress calculation to check the possibility to increase the force on the frame and on the rolls to improve mixing between components and evaluating the control of the total thickness.
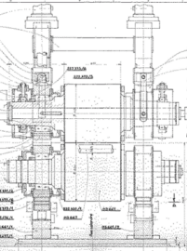
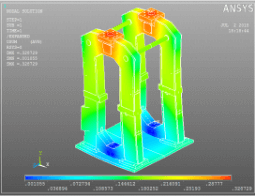
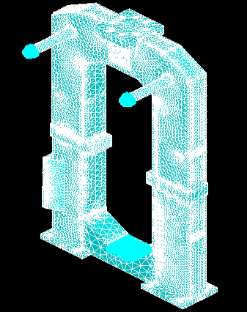
Creating a model by FEA of each frame side.
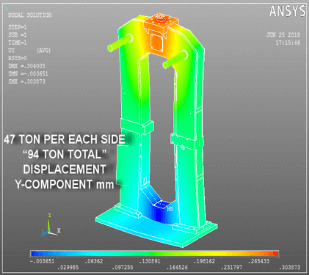
Stress calculation for each side.
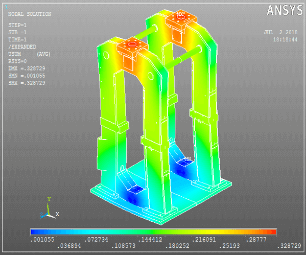
Stress calculation with both sides to control the whole machine reaction and validate the maximum clamping force applicable on each frame. For the project shown it has been calculated to go from 40T to 52T on each side.
Example 5
Modernization of 4 Rolls Calender 450 x 1000.
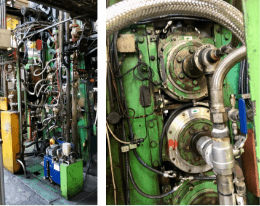
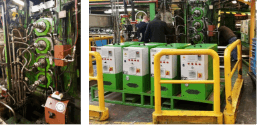
TCU replacement + Complete lubrication unit + Piping assembly for electrical and fluid connection.
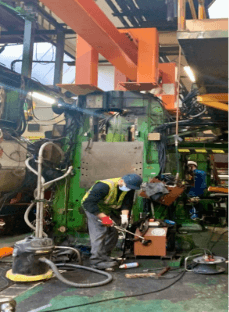
Manufacture of a custom-made gantry to ensure a quick replacement of parts on site.
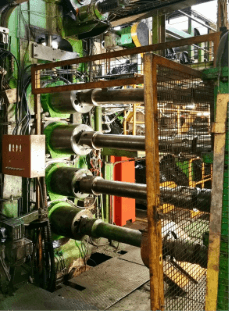
Transmission side view after replacement.
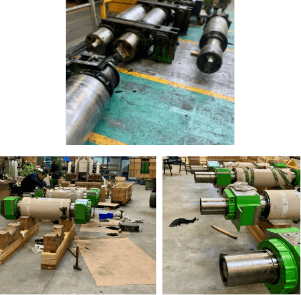
New Engineering Design + Replacement of Rolls + Bearings + Oil Seals + Flanges.
Front sensor replacement.
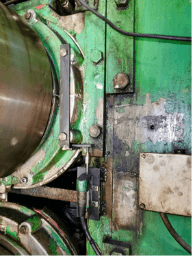
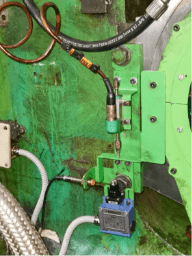